#160 Laboratorio VS campo (le influenze esterne)
La nostra specialità è quella di riuscire a reperire sul mercato qualcosa che spesso non si pensa che possa esistere. E non nascondo che siamo bravi a farlo. Chiaramente stiamo parlando di dispositivi di sicurezza o controllo della temperatura ma con esecuzioni o prestazioni molto particolari e al di fuori degli standard.
Il mondo si muove e cambia e la concorrenza può diventare spietata. Molti cercano di adeguarsi combattendo una durissima battaglia di riduzione dei prezzi, altri invece cercano di distinguersi proponendo soluzioni innovative o comunque diverse da quelle più tipiche. R&D Components può soddisfare entrambe le richieste. Le prime in realtà le può fare quasi chiunque, ma le seconde, quelle più stimolanti e impegnative non sono per tutti.
Conoscere, apprendere, camminare a fianco dei nostri clienti e diventarne partner in progetti destinati a cambiare, non dico il mondo, ma a volte il settore di appartenenza, ci trasmette sempre grande entusiasmo ed orgoglio per quello che alla fine riusciamo a fare. Non ci manca di certo l’esperienza, ma non sempre è sufficiente individuare un prodotto con le caratteristiche richieste. Perché la parte più complicata è quella di assicurarsi che queste performance siano mantenute anche in sede operativa.
Il DIN (Deutsches Institut für Normung – Istituto tedesco per la standardizzazione) è l’istituto che ha standardizzato i più importanti test necessari per procedere con un percorso di omologazione dei prodotti. Vengono definite le condizioni alle quali tali prove vanno effettuate nonché i modi e i tempi di esecuzione. Tutti i principali enti di omologazione si sono uniformati ai suoi dettami. Ma chiaramente e per ovvie ragioni, si tratta di una serie di test fatti in condizioni ottimali, in ambienti sterili e con tempi di salita della temperatura molto ragionevoli, per alcune prove si parla di 1°C al minuto. Quando vediamo su un catalogo o su una scheda tecnica un dato, questo è stato ottenuto e certificato da prove svolte seguendo passo passo quanto prescritto dal DIN. Ma è necessario fare molta attenzione quando un dispositivo viene applicato su un’apparecchiatura, soprattutto se questo è stato scelto per le sue prestazioni.
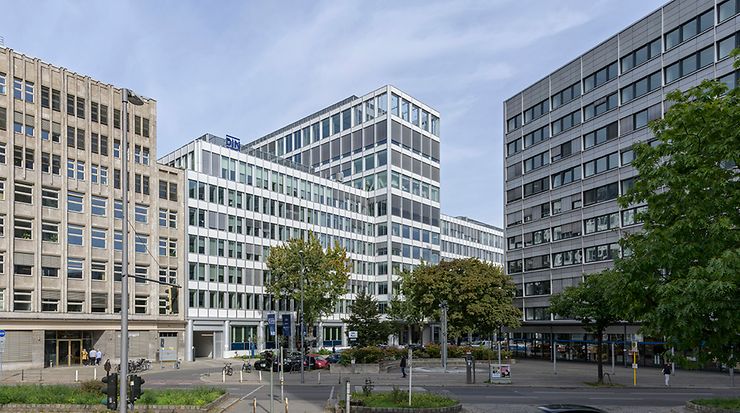
Fattori esterni
Esiste un numero altissimo di fattori esterni che possono portare una variante e influenzare negativamente il risultato. A seconda dell’applicazione e dello scopo del dispositivo possiamo avere influenze diverse e cercherò di farne un breve e sintetico elenco:
- Velocità nella salita della temperatura. In genere il sopracitato DIN prevede che per testare un dispositivo termico, termostato, termofusibile o protettore che sia, si debba partire da una situazione di temperatura ambiente (20-22°C) e salire di 1°C al minuto. Sul campo però le cose poi vanno diversamente e ci si potrebbe trovare ad affrontare un innalzamento della temperatura estremamente veloce tanto da passare da 20°C a 170°C in meno di 15 secondi con il conseguente fenomeno dell’inerzia termica. Ciò significa che un dispositivo che interviene correttamente a 170°C, si trova in un ambiente che nel giro di pochi secondi potrebbe raggiungere temperature che superano i 250°C. Questa è una situazione estrema per rendere più chiaro l’esempio. Se si sospetta che in fase di lavoro possa esserci una qualsiasi forma di inerzia termica, occorrerà considerare dei materiali resistenti ad essa.
- Ambiente di lavoro. Il luogo in cui il nostro dispositivo andrà a lavorare può esercitare un’influenza negativa fino a pregiudicarne il funzionamento. Non dipende solo da temperature particolarmente basse o eccessivamente elevate, ma anche dall’umidità o all’esposizione o meno a polveri.
- Presenza di materiali residui. Eventuali materiali sedimentati sul piano di lavoro su cui il dispositivo dovrebbe essere montato possono incidere su una errata lettura della temperatura e pregiudicarne l’aderenza.
- Aderenza: La maggior parte dei componenti di sicurezza termica lavorano a contatto e rilevano la temperatura per induzione di calore. Un’aderenza non perfetta può portare a una lettura imprecisa o tardiva. Dove possibile è bene, oltre che assicurarsi di applicare il dispositivo a regola d’arte, anche adottare la soluzione più adatta a seconda dei casi.
- Posizione. Molto importante è valutare dove il dispositivo sarà posizionato e comprendere tutte le condizioni di lavoro che influenzeranno quella posizione. Di seguito adattarsi ad esse scegliendo dispositivo ed esecuzione che possano lavorare senza variabili e nel modo in cui serve a raggiungere il risultato finale. La posizione può anche essere usata strategicamente per soddisfare una richiesta normativa nel momento in cui non vi è una risposta tecnica del prodotto sufficiente ad incontrare le imposizioni normative.
- Portata. La corrente di lavoro è molto importante, perchè ogni dispositivo ha un limite di portata alla quale i contatti possono resistere senza danneggiarsi. Ma non possiamo nemmeno trascurare il passaggio della corrente attraverso i contatti stessi. Questo perché, in seguito al cosiddetto effetto Joule, si può avere quello che viene definito declassamento e un dispositivo, in questo caso un protettore termico, si trova ad intervenire a una temperatura che risulta più bassa di quella d’intervento dichiarata.
- Ritardo termico. Si tratta fondamentalmente di una divergenza tra la temperatura effettiva nell’ambiente, o nel punto di lavoro, e quella che viene rilevata dal dispositivo. In genere può essere determinata da materiali di costruzione eccessivamente isolanti, che possono proteggere da temperature più elevate ma sono meno sensibili alla rilevazione termica. Oppure più economici, ad esempio un protettore termico con corpo plastico in genere ha un lieve ritardo termico se paragonato a uno col corpo metallico. In questo caso è importante valutare attentamente se tale ritardo possa manifestarsi e se in tale caso sia tollerabile o meno e a quali livelli.
- Posa in opera: Può sembrare un passaggio banale, ma installare un prodotto nel modo corretto è fondamentale per avere il funzionamento desiderato. Non sono molte le precauzioni che si devono prendere ma non esiste tolleranza in questa fase. Quello che accomuna praticamente tutti i dispositivi è la necessità che vi sia una perfetta aderenza al piano su cui sarà applicato. Salvo il caso in cui la rilevazione non sia in aria, come ad esempio accade con frequenza per i termofusibili. Se invece consideriamo un termostato bimetallico con un fissaggio a vite, potremmo essere portati, in fase di montaggio, a fare forza sui terminali. Oppure, per semplificarci il lavoro, a piegarli, o ancora a sforzare una rotazione del corpo del termostato per orientare i terminali a nostro piacimento. Questo è molto pericoloso perché potrebbe aumentare sensibilmente le possibilità di staratura del componente. Anche i protettori termici hanno le loro fragilità, ad esempio nel modo in cui si maneggiano i cavetti, perché bisogna evitare che possano essere danneggiati.
- Resistenza a compressione. Se un protettore, anziché essere alloggiato in un apposito spazio disegnato sulle sue dimensioni viene inserito all’interno di un avvolgimento, sarà necessario assicurarsi che il dispositivo abbia la capacità di resistere a quella forza di pressione sul suo corpo se non vogliamo avere spiacevoli sorprese.
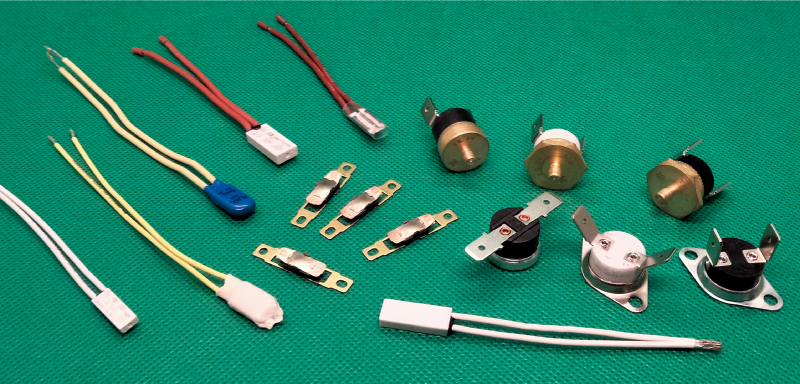
Questi sono solo alcuni esempi dei fattori che dobbiamo tenere in considerazione nel momento in cui andiamo a scegliere un prodotto da usare nella nostra applicazione, e la dura scelta spetta al responsabile tecnico.
Noi siamo qui, e siamo sempre al vostro fianco, pronti a mettere oltre venticinque anni d’esperienza al vostro servizio per proporvi o consigliarvi la soluzione più idonea. A volte è a portata di mano, a volte è qualcosa di nuovo e mai affrontato prima e a quel punto ci mettiamo alla ricerca, studiamo, valutiamo e, molto spesso, troviamo e a quel punto impariamo e cresciamo. La nostra storia è un perpetuo cammino verso un costante miglioramento che non avrà mai fine.